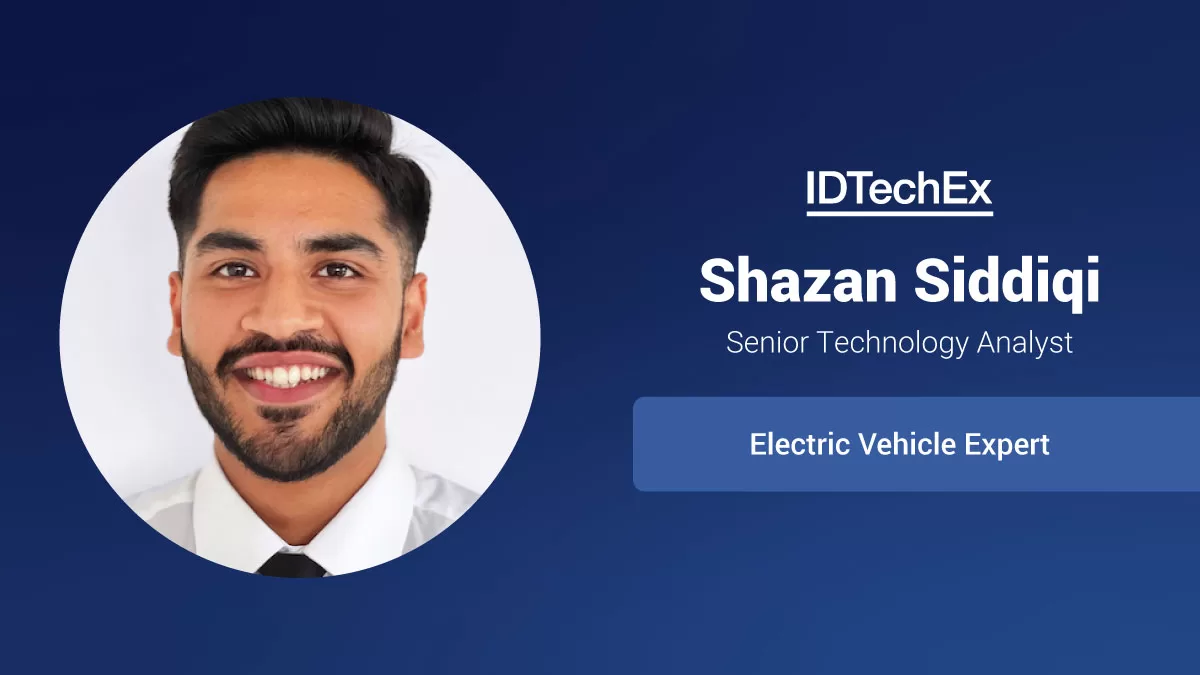
Author: Shazan Siddiqi, Senior Technology Analyst at IDTechEx Global efforts to decarbonize medium- and heavy-duty (MHD) freight vehicles are crucial for reducing transportation-related greenhouse gas (GHG) emissions. These vehicles, pivotal to economies worldwide, emit significant GHGs and criteria pollutants, often impacting vulnerable communities. Fortunately, a growing array of technologies can eliminate tailpipe emissions and reduce the overall carbon footprint of MHD vehicles. Currently, over 160 models of zero-emission trucks are available from more than 40 original equipment manufacturers (OEMs), which are benchmarked on various performance metrics in IDTechEx’s latest report, “Electric and Fuel Cell Trucks 2024-2044: Markets, Technologies, and Forecasts”. MCS is the peak of cable-based conductive charging for trucks Most commercial vehicle charging today is limited to between 150 and 350 kW. While charging at this level meets the needs of many fleets, as the use of commercial battery electric vehicles expands, there will be use cases that will benefit from higher-powered charging, adding hundreds of miles of range to a heavy-duty truck during a rest break. IDTechEx research finds that the megawatt charging system (MCS) presents opportunities and challenges of moving to much faster charging speeds, but predict that it will become the exclusive commercial vehicle charging standard. The MCS associated voltage cap is 1250 V, so it is evident that higher charging powers are achieved by higher current and not voltage for commercial vehicles. MCS increases current by 600% and voltage by 20%, and this brings about new thermal management challenges. Active cooling of the cable and connector is required, and at power levels over 3 MW, the vehicle inlet will also require cooling. Additional challenges also exist. Truck OEMs buying battery packs from third-party suppliers need to make sure voltage requirements meet the specs of MCS. Furthermore, supplying power to the site of groups of these chargers can be challenging, specifically with long lead times on interconnection agreements, transformers, and permits, as well as demand fees. While MCS will become the standard in Europe and the US, In China, co-developers China Electricity Council, and CHAdeMO’s “ultra ChaoJi” are developing a charging standard for heavy-duty electric vehicles for up to 1.8 MW.
|
||
IDTechEx research finds several coupler manufacturers, EVSE manufacturers and several vehicle manufacturers in the MCS player landscape. Source: IDTechEx – “Electric and Fuel Cell Trucks 2024-2044: Markets, Technologies, and Forecasts” |
||
The rise of battery swapping in the Chinese truck market Battery swapping has the shortest charging downtimes (~3-6 minutes) of all charging strategies. For many Chinese trucks, the battery is behind the cab, in a swappable box that can be lifted and moved to the side. Almost all heavy swap-capable trucks in China use a CATL 282 kWh LFP pack (weighing 3.2 tonnes), which has helped solve the issue of standardization when trying to implement swapping. Swap-capable electric trucks are mainly used for short-haul applications (less than 100 km) at ports, mining sites, and in urban logistics that require a quick turnaround time. Battery swapping in China is a product of increased policies – targets laid out by the central government and subsidies provided for swap station construction (up to 15%) by the local government help alleviate the issues around high capital costs associated with large swapping stations. IDTechEx research finds that battery-swapping trucks are now taking up roughly 50% of the electric truck market in China. The swap stations can act as grid support units and help reduce the upfront sticker price of trucks by using the battery as a service (BaaS) business model where the costs of the truck and battery are decoupled. This is particularly helpful for fleet owners for whom the TCO of going electric now makes the most economic sense. However, IDTechEx finds that taking into account depreciation, impairment, site rent, kilowatt-hour electricity costs, and labor costs, the investment payback period for a heavy-duty truck battery swapping station is as long as 6 years. Given the high initial upfront capital cost, unless there is significant government support and OEM interest in the swapping charging strategy for trucks in the Western world, this technology will remain dominant in China.
|
||
The battery swapping ecosystem for trucks in China. Source: IDTechEx |
||
IDTechEx’s latest report, “Electric and Fuel Cell Trucks 2024-2044: Markets, Technologies, and Forecasts”, covers the spectrum of EV charging strategies being considered for successful heavy-duty fleet transition to electric. It includes analysis of private depot AC charging, MW public charging, battery swapping, and dynamic wireless charging. It considers different duty cycles across various logistics scenarios and presents optimum charging technologies best suited for each case. To find out more about this IDTechEx report, including downloadable sample pages, please visit www.IDTechEx.com/trucks. |